Author |
Topic  |
|
pauly45
United Kingdom
435 Posts |
Posted - 04/04/2017 : 19:55:41
|
Hi, Perhaps someone with more experience with a lathe could advise me on how I machine up an accurate 'thin' washer such as the phosphor bronze washer behind the cam bevel gear, and also the thin rocker spacers.
By thin I mean about 4mm or less (down to about 1mm).
I'm fine with machining the outer diameter, inner bore, front face and then parting that off.
But once that 'washer' is parted off, how do you then hold that to machine the other face to an accurate thickness?
A wouldn't have thought a 3-jaw chuck would be accurate enough to hold it square, so do I need to use a Step Collet, machine into that a recess the same diameter as the washer I am creating and then pop it in and nip it up to machine to an accurate thickness?
Thanks Paul |
Edited by - pauly45 on 04/04/2017 19:57:45 |
|
nigel stroud
United Kingdom
110 Posts |
Posted - 04/04/2017 : 20:31:59
|
Hi Paul, I recently made up some shims in brass. I parted off at about .5mm then stuck the machined face to a larger dia. mandrill with superglue then carefully machined down to the required thickness. Removal is the tricky bit but they came off with a well aimed tap! Hope this helps. Rgds nigel |
 |
|
graham3647
United Kingdom
448 Posts |
Posted - 04/04/2017 : 20:43:37
|
Hello, If you can buy a set of soft jaws for the chuck on your lathe then you need to buy a set, They are not expensive. The next step is to replace your hard jaws with the soft jaws. Chuck jaws are numbered 1 to 3. The numbers are also stamped on the chuck face. Find the start of the chuck scroll and insert the jaws in numerical order. The next step is to machine the jaws to take your spacer only enough to grip the spacer. If you do this correctly, the spacer will run true. You can then machine your spacer to he correct dimension. Most centre lathe turners use soft jaws frequently and you will too after using them. Best of luck. Graham. |
 |
|
rustcollector
United Kingdom
411 Posts |
Posted - 04/04/2017 : 23:11:33
|
Why don't you just machine as you suggested and then part off to required thickness.
Machine the Id and od to size , remove sharp edges, measure parting tool width, face off front edge , set dial to zero , move tool out from job and advance parting tool width plus thickness required , lock carriage and part off , debur and use .
That is the way a machinist would carry out the job
It's not going to work by trying to hold in a chuck.
How many are you going to make |
Edited by - rustcollector on 04/04/2017 23:17:43 |
 |
|
coracle
United Kingdom
1970 Posts |
Posted - 05/04/2017 : 01:08:40
|
Google "machining a thin washer" and select your preferred method. |
 |
|
pauly45
United Kingdom
435 Posts |
Posted - 08/04/2017 : 21:17:02
|
Hi,
Thank you all.
Today I trialled the method suggested by Nigel - machined up a piece of aluminium and superglued the piece to it. It allowed me to very quickly turn down the washers I needed - the smallest being 0.42mm Dead easy to do really once you know how!
The soft jaws for the chuck are pretty much the same idea as the step collet.
Many thanks for all your inputs. Paul.
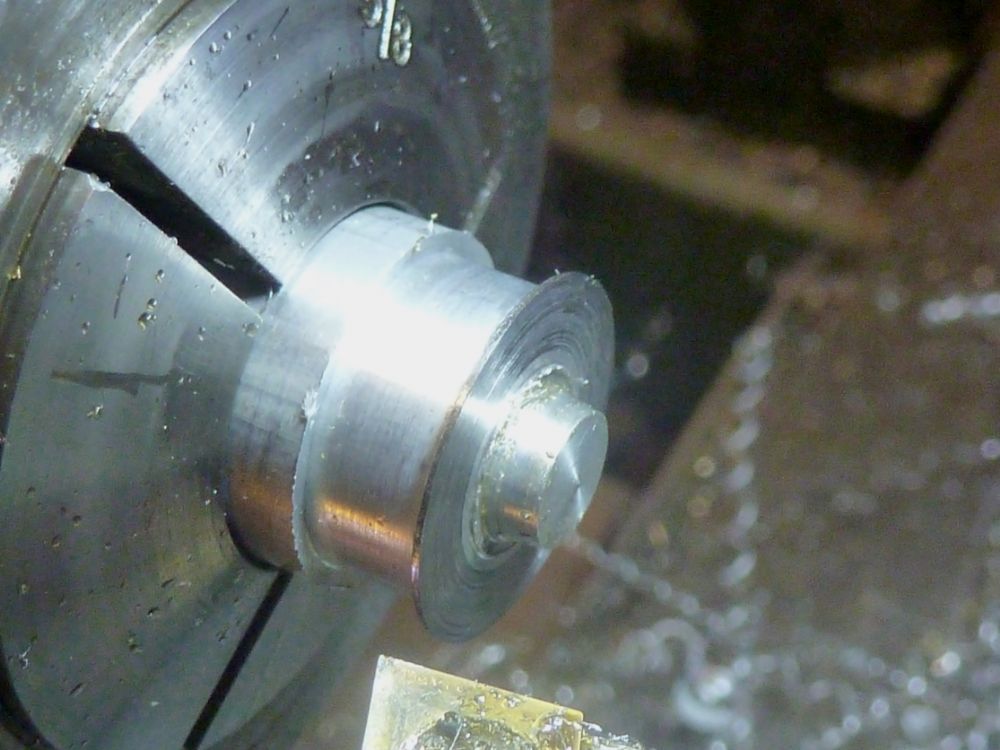 |
 |
|
DDMDSN
New Zealand
329 Posts |
Posted - 09/04/2017 : 01:50:02
|
Suitable micro-lathe can also help accuracy of machining and part-off. Three jaw chuck works fine on a micro lathe. I use a Proxxon PD250 micro-lathe with .05mm division hand dials. Well sharpened and suitable profile cutting tools also help accuracy and finish. For exact thickness as needed for eg camshaft thrust washer, can lap the washer. Easiest way is to glue the washer to a flat piece of glass, and glue fine wet and dry SiC paper flat to another piece of glass. Lap using fine oil eg carburettor/sewing machine oil as a lubricant. This can provide accuracy to less than 1 thou. Use micrometer to check thickness. Donald PB0759 |
 |
|
DDMDSN
New Zealand
329 Posts |
Posted - 09/04/2017 : 11:20:48
|
Proxxon PD250 micro-precision lathe parting-off 1mm rivet burr from 1040 carbon steel. The smaller the diameter and softer the material, the faster the speed required for a clean cut, aluminium being about the softest, with brass then bronze next. Untempered 1040 carbon steel about the hardest this lathe will cut using the regular high speed steel cutting tools. Cutting tools must be kept really sharp. I use a high speed micro grinder. Donald PB0759
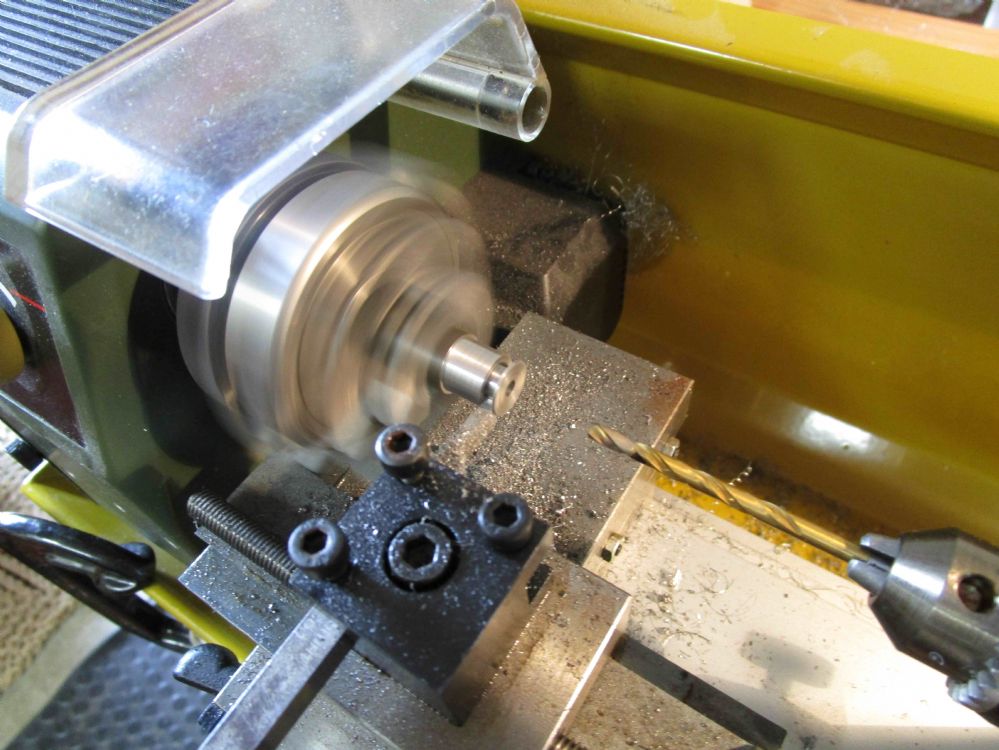 |
 |
|
Gerhard Maier
Germany
880 Posts |
|
|
Topic  |
|