Author |
Topic  |
|
pauly45
United Kingdom
435 Posts |
Posted - 11/09/2016 : 08:08:12
|
Hello,
I thought I would share a little project I have been working on.
Having failed to find another undamaged gearstick turret for my P-Type, or get the one I have repaired, I have been trying a different approach.
The mechanical engineer at work has kindly created me a 3D CAD model of the turret and we have 3D printed it.
I'm now on the second version, and there are a few more tweaks needed to it. The photos are of the printed turret removed from the support structure that the printing process created, together with it painted.
My plan, at least initially, is to machine in a small metal bush in the bottom where the gearstick ball sits and use it.
I know it is not perfect, fragile and a bit brittle in the plastic it has currently been printed in, but it is still better than the one I have.
The bonus is that I have the 3D CAD model and once I'm happy with it I will get a cost for 3D printing in aluminium. That should be interesting!
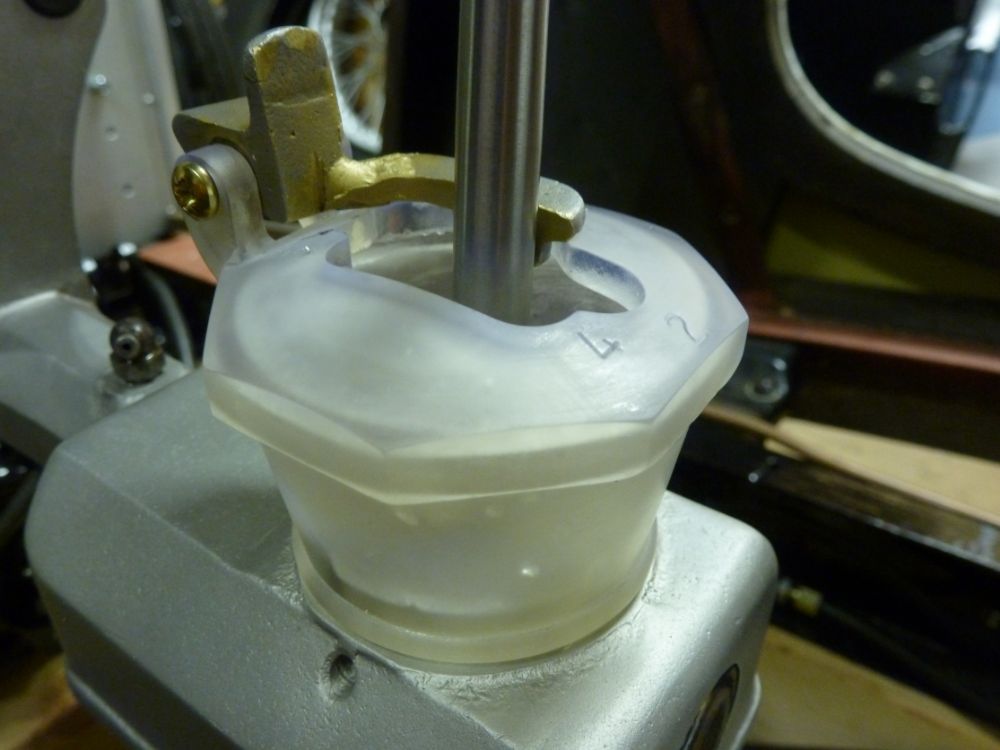
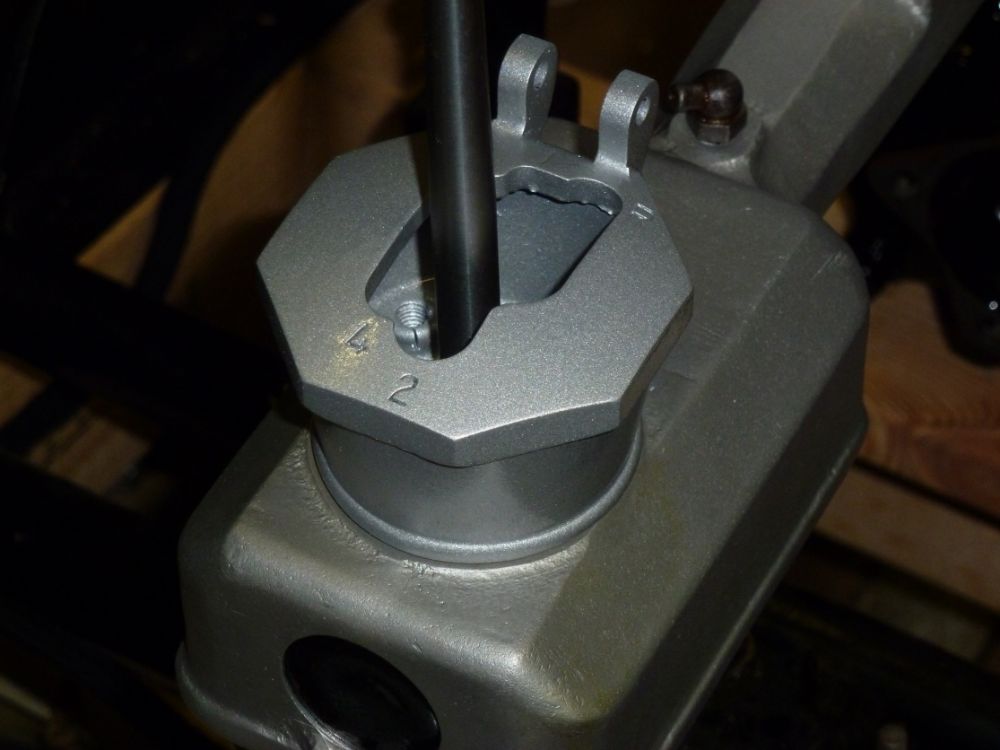
Paul |
Edited by - pauly45 on 11/09/2016 08:10:13 |
|
DDMDSN
New Zealand
329 Posts |
Posted - 11/09/2016 : 08:34:32
|
Nice jobPaul! This is also a part I need. Saved by a new gear lever last time however so much wear around the ball that will start to pop out of in 2nd gear again sooner or later. I'm working on some 3-part casting resin moulds with insert suitable for investment casting as I believe ideal (fine detail and accuracy) for for the MMM dashboard grab handle, SF24 trafficator arm, and knock-off wheel hammer head let the forum know how I get on. This method would suit the remote gear tower too reckon. With removable mould inserts, allows for internal shapes. Yes, my reverse gate also broke (a second time after brazing), made one from solid brass. Donald PB0759 |
 |
|
DDMDSN
New Zealand
329 Posts |
Posted - 12/09/2016 : 00:02:11
|
Further thoughts. Paul, most interested in the feasibility and price to 3D print in aluminium, will watch out for news. Interested in how were made originally, anyone know? To investment cast, my thinking is to make in 2 halves each with a 2 part die, then weld and hand finish the wax forms together, before casting. Bit like making a bronze sculpture with internal 3D detail. As far as I am aware yet to be successfully reproduced, I suspect quite challenging. Donald PB0759
|
 |
|
Ian Bowers
United Kingdom
941 Posts |
Posted - 12/09/2016 : 07:49:51
|
If you are going to use as a mould for casting, you need to oversize to allow for shrinkage (2% for steel and 1.5% for aluminium alloys), and unless it is for investment (lost wax) casting, to work out the split lines to remove from a sand mould.
Ian Bowers OD 6791 J3 3772 |
 |
|
Bodger
United Kingdom
65 Posts |
Posted - 12/09/2016 : 11:47:42
|
Well done Paul I think this is a part that many people wish was available, me for one. As an alternative to 3D printing Aluminium, it looks possible to 3D print wax and use this for investment casting. This would allow the whole part to be produced as one piece of wax.
Jonathan Welch |
 |
|
George Eagle
United Kingdom
3237 Posts |
Posted - 12/09/2016 : 12:44:54
|
Amazing technology - I wonder how long before someone produces a K3 lookalike!
George L2023 |
 |
|
pauly45
United Kingdom
435 Posts |
Posted - 12/09/2016 : 12:45:27
|
Thanks.
A further bit of tweaking has been done - a slight re-profile of the gear stick opening and the internal bosses for the mounting bolts.
I still need to find a better number font that is the right shape and boldness.
I had thought about the possibility of printing a mould to allow casting to occur. We will see..
I will try the aluminium printing route first and see where that goes.
As with most things, the more that are made, the cheaper each individual item becomes. Usually.
Paul. |
 |
|
BobH
United Kingdom
250 Posts |
Posted - 12/09/2016 : 14:39:26
|
That doesn't follow with 'additive manufacture' as the engineers prefer to call it. The space in the metal-sintering machine is usually a fixed volume so its easy to add an extra small component into a build, in a space which would otherwise be unused. Added cost is minimal even for a one-off - just the time for inclusion of the CAD file and clean-up of the component afterwards. |
 |
|
sullivan
USA
423 Posts |
Posted - 12/09/2016 : 21:14:24
|
My car, PA 1024 was early production 5th May 1934.
Seems that others have a one piece turret? I noticed when the gear shift lever sheered off on PA1024 and I removed the lever, that the upper part of the casting the "lid" (hexagon top) was a separate threaded part from the "collar" or tapered tube section. I was able to simply un-twist this threaded section. Is this different that other's Turrets ?
Kindly,
Brian W Sullivan |
 |
|
DDMDSN
New Zealand
329 Posts |
Posted - 12/09/2016 : 21:31:30
|
Interesting ideas. Casting method proposing is lost wax. I am going in to get some test investment castings done on my other items in 3-4 weeks will check feasibility on this method on this item, and for recommended shrinkage allowance for aluminium (get shrinkage on both the metal and in the moulding). Preferred method I suspect will depend on cost, time, and ultimately demand for the end item. The big part of lost wax is making the 2-part moulds (one for each side) which I can make. Once done is quite straight-forward and cost effective for multiple castings (up to about 100 I gather for casting resin and metal insert moulds). I suspect that when the two wax halves are joined, the wax itself would need to be cleaned up at the join, prior to ceramic coating and then the casting. |
 |
|
Ian Bowers
United Kingdom
941 Posts |
Posted - 13/09/2016 : 07:36:11
|
It is going to be more than a two part casting, to take account of the lugs and the hexagon overhang!
Ian Bowers OD 6791 J3 3772 |
 |
|
DDMDSN
New Zealand
329 Posts |
Posted - 13/09/2016 : 21:38:56
|
Ian, yes, to avoid extra machining, would need to be made in right and left male/female with inserts each for wax moulds. One insert for the reverse lever tab, and one for the underside ball joint. The two wax halves would need to be joined and cleaned up ready for ceramic coating then casting. Attached photo of my gear lever turret, with hand made reversing gate made from solid. Ball joint wearing and saved by a new gear lever, was popping out and jamming in second before that. Believe the J type is the same without the reverses gate tabs. I think after my current investment casting projects, may be ready for the gear lever turret, a really difficult one, next year if there is still a need for a version to be made. Enjoy hand making the moulding blocks which I carve by hand in wood, same way I suspect as the originals complete with minor imperfections. Attached the blocks I am making for the lead knock-off hammer head. The handle will be an insert for investment casting. Found someone set up to cast lead. Donald PB0759
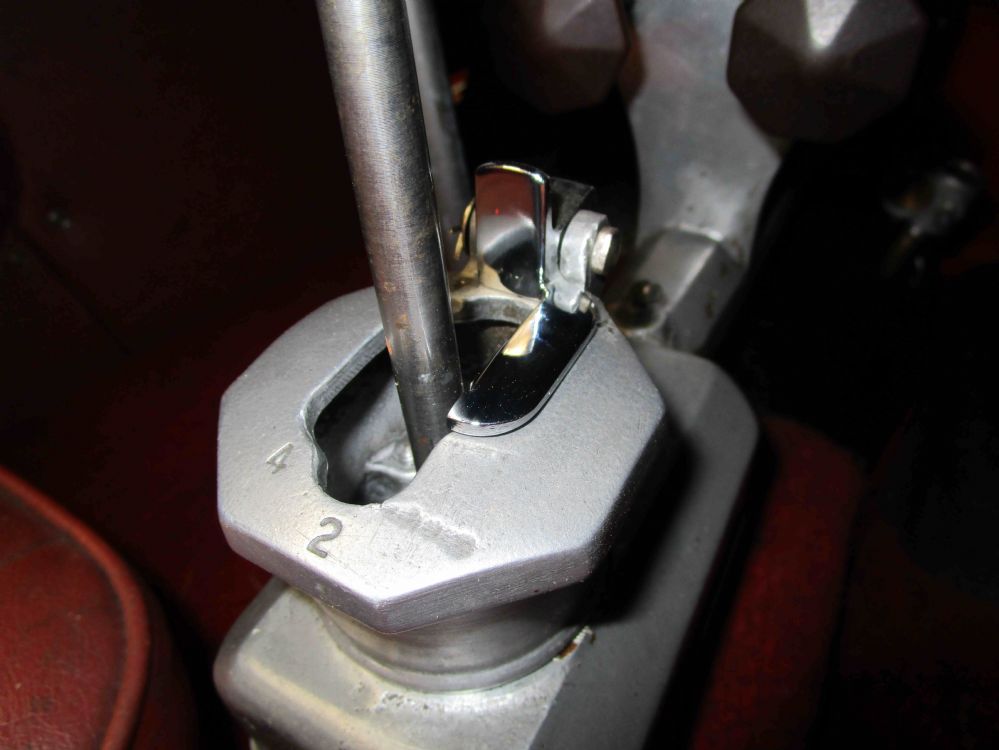
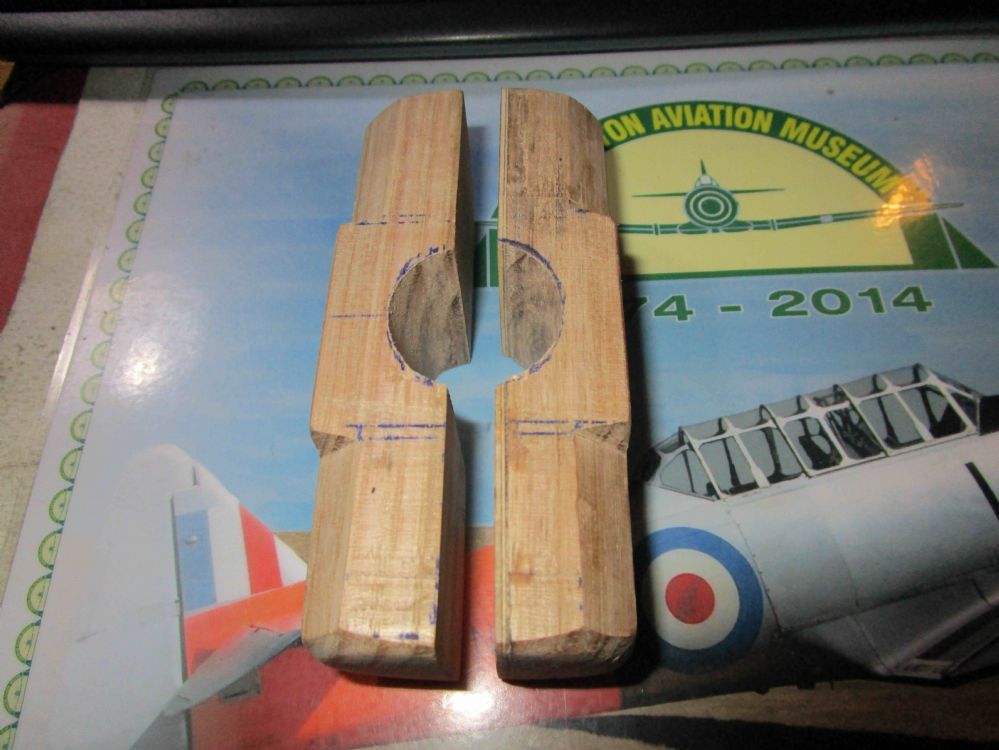 |
 |
|
Andrew Fock
Australia
374 Posts |
Posted - 18/09/2016 : 02:20:21
|
Hi Don,
I've previously discussed this with one of my Engineer mates who says the way to go at the moment would be 'lost plastic' casting as the cost of printing in aluminium is still too high but you can get the item printed in a low heat plastic quite cheaply....
regards,
Andrew
|
 |
|
|
Topic  |
|